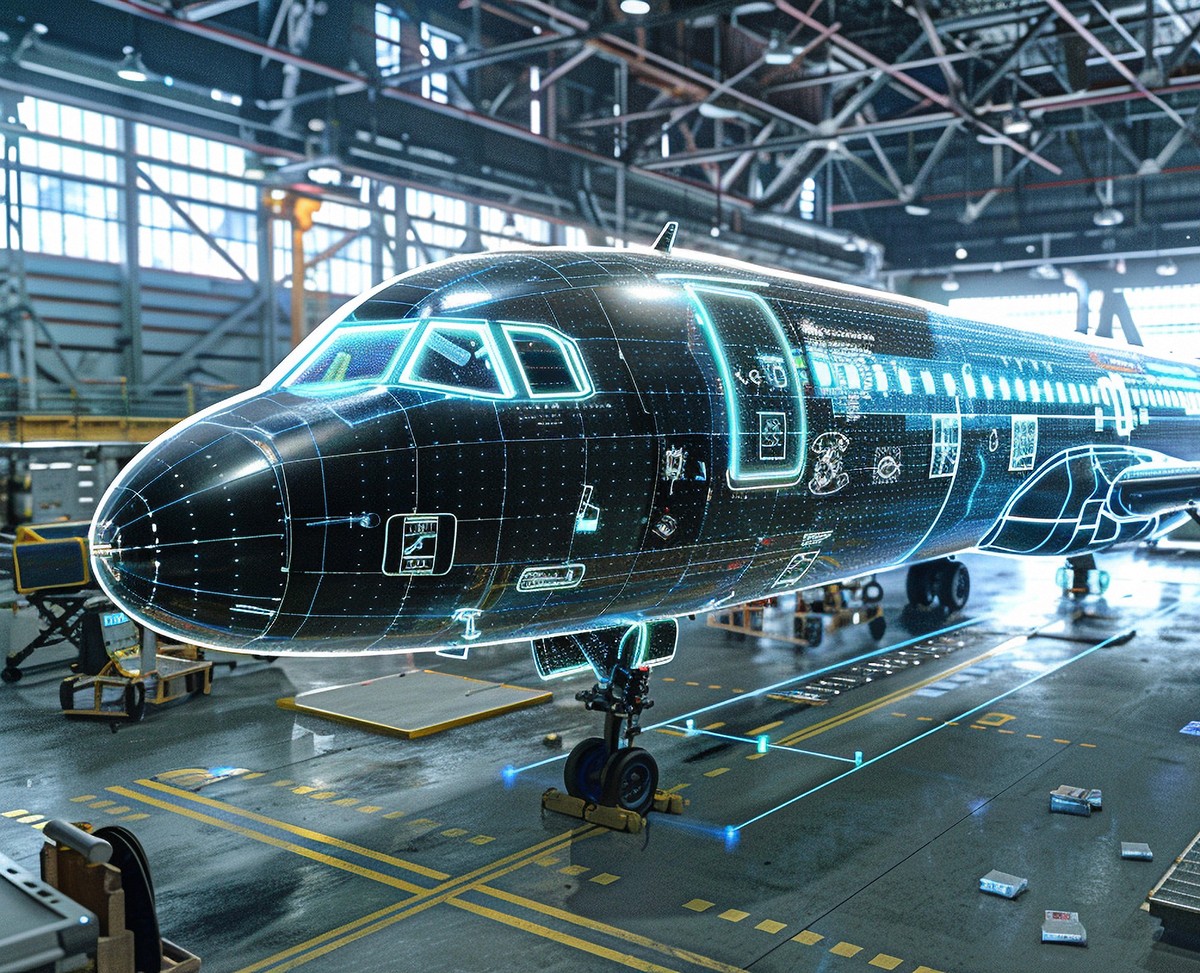
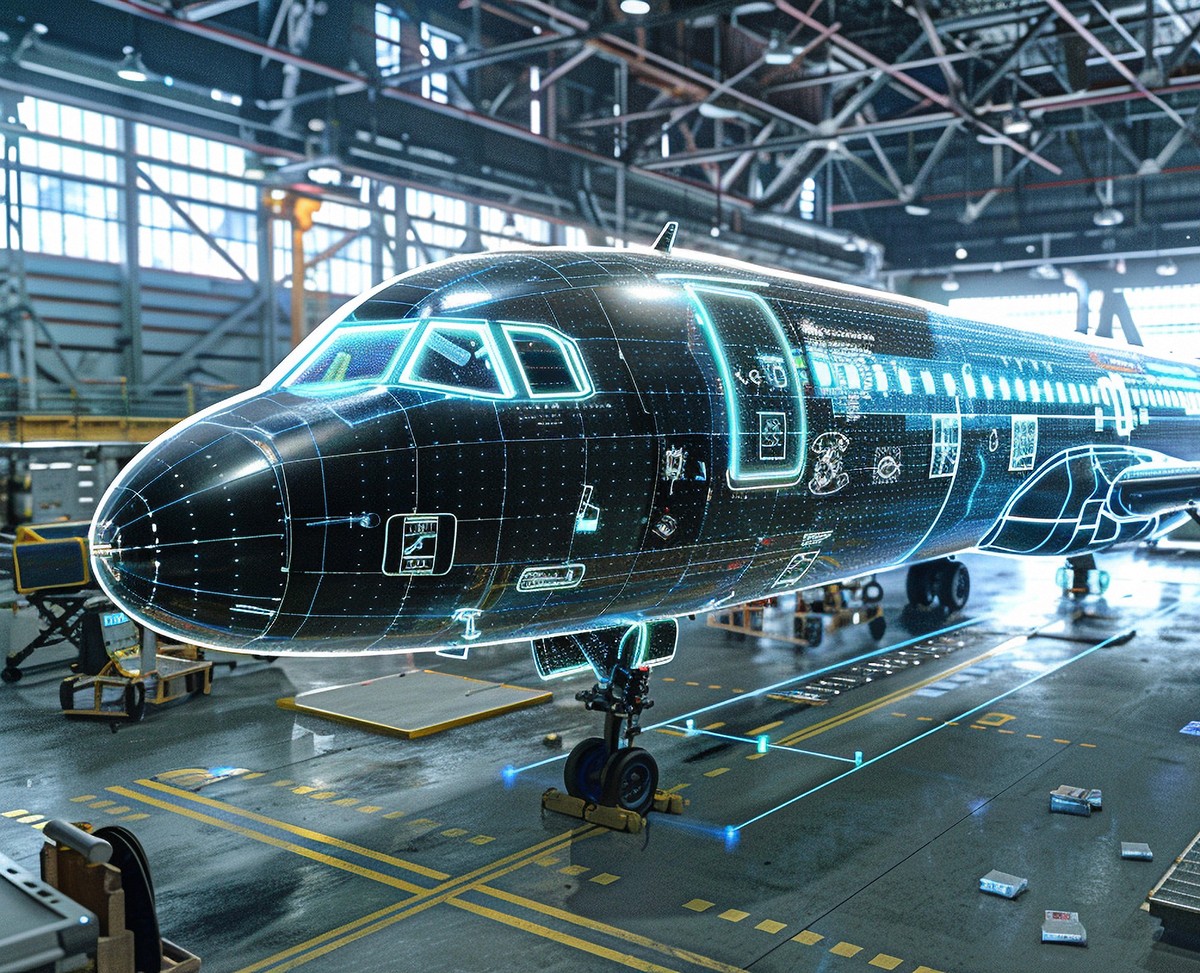
AIRCRAFT OEMs, Service Providers and Carriers
Go-to-market approach for AR-assisted Maintenance, Repair and Overhaul (MRO)
The use of Extended Reality (XR) is on the verge of large-scale adoption for enterprise use cases. A flurry of advances to headsets and components, involvement of a growing number of trusted software and hardware innovators, more tools available for content creators, and advances in tangential technologies including IoT, 6G and AI are all combining to provide capabilities that can deliver value. With such a broad set of possibilities, choosing an initial industry and focus area is a fundamental challenge.
Through discussion with industry leaders, our team determined that the aircraft Maintenance, Repair, and Overhaul (MRO) industry faces significant challenges, and integrating Augmented Reality (AR) could address many of them. Financial models were used to forecast MRO work across OEMs, carriers and MRO companies as the basis for projected savings due to reduced downtime. Organizations that have already moved to “mobile maintenance” would be likely adopters of AR as a way to leverage their existing investment.
We developed supporting go-to-market materials that outlined the market opportunity, specific scenarios that highlighted the value of augmented reality and an existing project plan for a series of engagements to deliver a functioning augmented reality experience that would deliver value and efficiency.
Specific challenges addressed in our scenarios and storyboards included:
Complexity of Maintenance Procedures—Aircraft systems are highly complex, requiring precision and adherence to stringent regulatory standards. MRO teams often work with detailed manuals and checklists. AR can provide real-time visual guidance and overlay step-by-step instructions on physical components, helping technicians follow procedures accurately without needing to refer to physical manuals.
Skill Gaps and Training—The aviation industry faces a shortage of highly skilled technicians, and training new hires is time-consuming and costly. AR can offer immersive, on-the-job training by simulating real-life scenarios and allowing trainees to practice virtually. This also reduces the burden on experienced technicians in the onboarding experience.
Error Reduction and Efficiency—Human error is a major concern in MRO activities. Misinterpretations or skipped steps can lead to costly and dangerous mistakes. AR can reduce errors by visually verifying each completed task in real time. Overlaying data on equipment helps technicians see immediate feedback on their work, improving accuracy and minimizing mistakes.
Access to Real-Time Data—MRO teams often need access to large volumes of data, including service bulletins, repair histories, or sensor data, which can be difficult to manage during operations. AR systems can pull up real-time sensor data or maintenance records directly into the technician’s field of view, allowing them to diagnose issues more efficiently without interrupting the workflow.
Remote Assistance—When dealing with complex repairs in remote locations or requiring specialized expertise, teams often struggle to get timely support. AR-powered remote collaboration allows experts to “see” what the technician is seeing and provide detailed, real-time guidance, potentially reducing downtime and improving problem-solving.
Regulatory Compliance and Documentation—Ensuring that every step of the maintenance process is documented for regulatory compliance is vital. AR systems can automatically track and record each action taken during maintenance, ensuring that proper documentation is created without manual intervention. This helps streamline regulatory compliance efforts.
The use of Extended Reality (XR) is on the verge of large-scale adoption for enterprise use cases. A flurry of advances to headsets and components, involvement of a growing number of trusted software and hardware innovators, more tools available for content creators, and advances in tangential technologies including IoT, 6G and AI are all combining to provide capabilities that can deliver value. With such a broad set of possibilities, choosing an initial industry and focus area is a fundamental challenge.
Through discussion with industry leaders, our team determined that the aircraft Maintenance, Repair, and Overhaul (MRO) industry faces significant challenges, and integrating Augmented Reality (AR) could address many of them. Financial models were used to forecast MRO work across OEMs, carriers and MRO companies as the basis for projected savings due to reduced downtime. Organizations that have already moved to “mobile maintenance” would be likely adopters of AR as a way to leverage their existing investment.
We developed supporting go-to-market materials that outlined the market opportunity, specific scenarios that highlighted the value of augmented reality and an existing project plan for a series of engagements to deliver a functioning augmented reality experience that would deliver value and efficiency.
Specific challenges addressed in our scenarios and storyboards included:
Complexity of Maintenance Procedures—Aircraft systems are highly complex, requiring precision and adherence to stringent regulatory standards. MRO teams often work with detailed manuals and checklists. AR can provide real-time visual guidance and overlay step-by-step instructions on physical components, helping technicians follow procedures accurately without needing to refer to physical manuals.
Skill Gaps and Training—The aviation industry faces a shortage of highly skilled technicians, and training new hires is time-consuming and costly. AR can offer immersive, on-the-job training by simulating real-life scenarios and allowing trainees to practice virtually. This also reduces the burden on experienced technicians in the onboarding experience.
Error Reduction and Efficiency—Human error is a major concern in MRO activities. Misinterpretations or skipped steps can lead to costly and dangerous mistakes. AR can reduce errors by visually verifying each completed task in real time. Overlaying data on equipment helps technicians see immediate feedback on their work, improving accuracy and minimizing mistakes.
Access to Real-Time Data—MRO teams often need access to large volumes of data, including service bulletins, repair histories, or sensor data, which can be difficult to manage during operations. AR systems can pull up real-time sensor data or maintenance records directly into the technician’s field of view, allowing them to diagnose issues more efficiently without interrupting the workflow.
Remote Assistance—When dealing with complex repairs in remote locations or requiring specialized expertise, teams often struggle to get timely support. AR-powered remote collaboration allows experts to “see” what the technician is seeing and provide detailed, real-time guidance, potentially reducing downtime and improving problem-solving.
Regulatory Compliance and Documentation—Ensuring that every step of the maintenance process is documented for regulatory compliance is vital. AR systems can automatically track and record each action taken during maintenance, ensuring that proper documentation is created without manual intervention. This helps streamline regulatory compliance efforts.
Market Research
Projected spending for MRO work at leading organizations over the next 12, 24 and 36 months to create a model that was the foundation for calculating impact
Identifying Current Pains
A generalized MRO process was used to frame areas that would benefit most from hands-free guidance and real-time support
Storyline Creation
The team focused on key moments and know frictions to illustrate how in-context help and AI could make workers more effective
Collaboration with Experts
Interviews and workshops with experts in the aircraft MRO field provided high-value scenarios and refinement
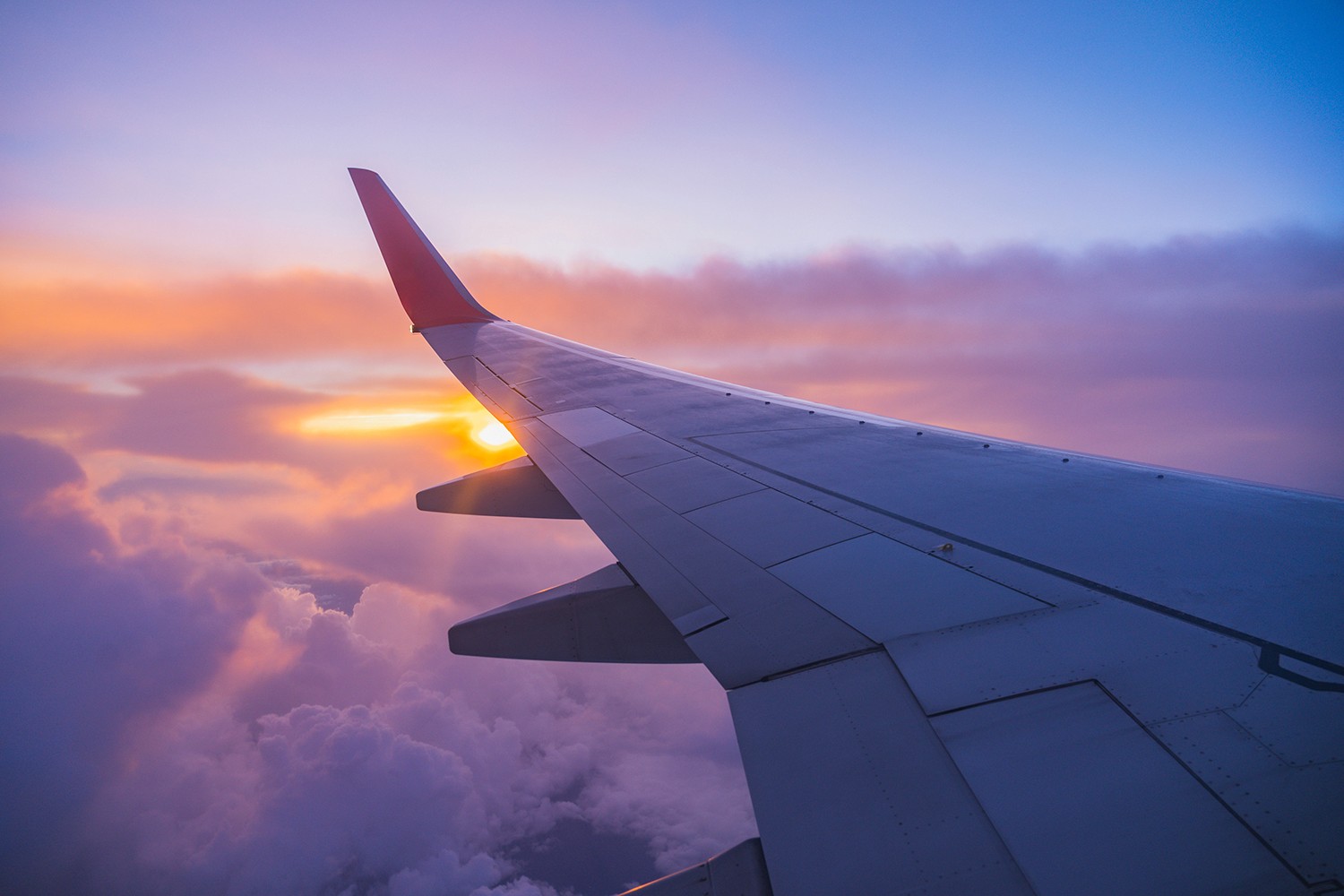
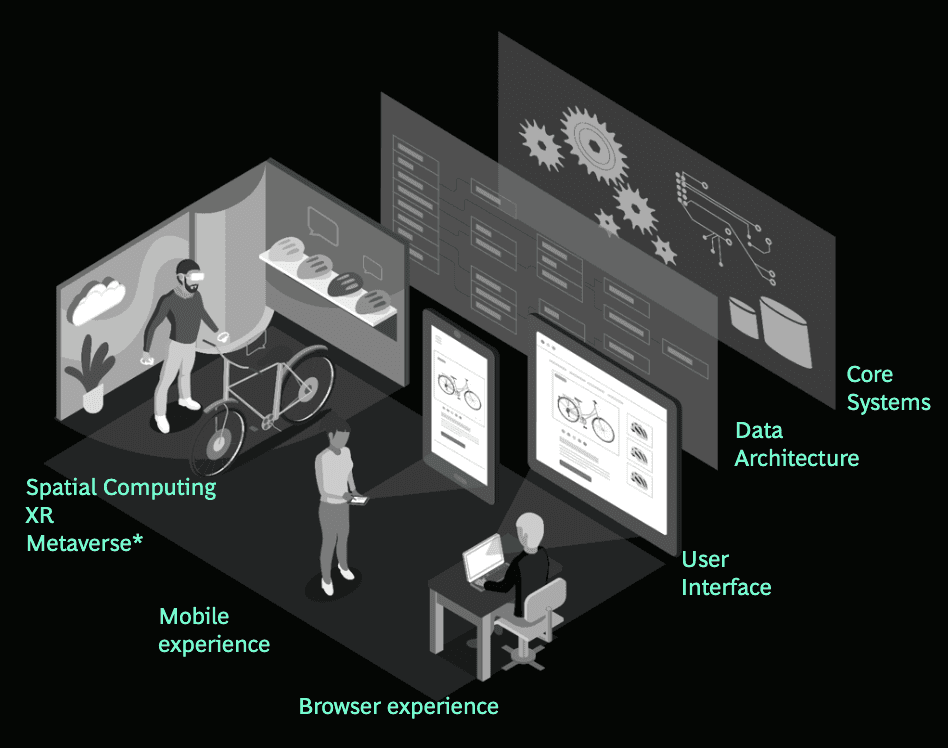

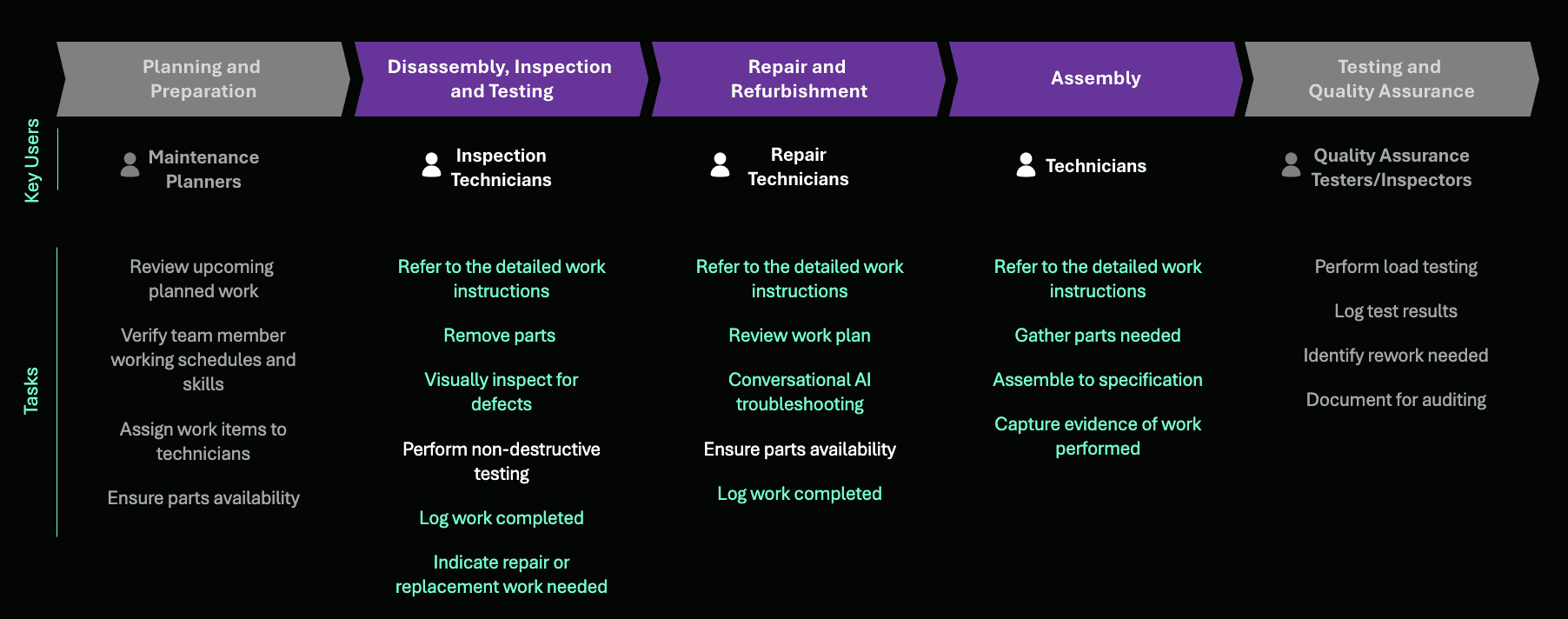
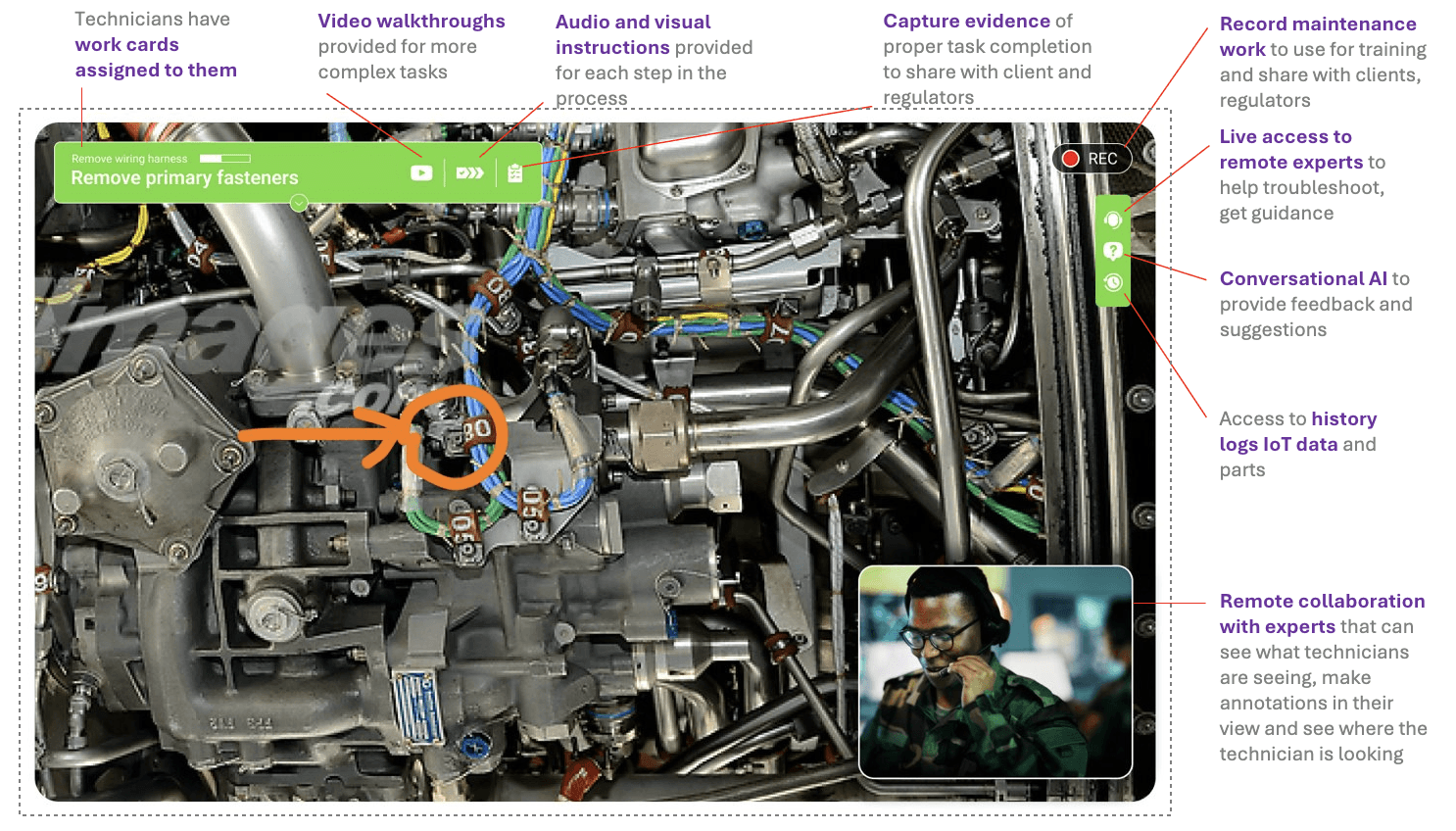

Impact
Value Case
Financial impact was modeled using workforce data, spending forecasts and the projected gains from reduced downtime
High Value Scenarios
Specific use cases from SMEs tied the value case to known current state challenges
Sales Materials
Presentations, storylines and data were tailored to the MRO industry and C-level audience to support early stage discussions
© 2025 Mark Lotter
© 2025 Mark Lotter
© 2025 Mark Lotter